Galway based 3D Technology Ltd. sees demand surge for 3D printing solutions in Ireland
Stanley Black & Decker, an S&P 500 company, is a diversified global provider of hand tools, power tools and related accessories, electronic security solutions, healthcare solutions and engineered fastening systems.
Stanley Infrastructure, a division of Stanley Black & Decker, is focused on ways to manufacture low volume, complex parts in a cost efficient manner. By leveraging Markforged’s Metal X additive manufacturing technology, the Infrastructure team is slashing capital costs on a range of various parts, including an actuator housing for the PD45 Hydraulic Post Driver.
Just like many manufacturing companies here in Ireland, engineers at Stanley Infrastructure are rigorously testing the performance, durability and life cycle of 3D printed parts to replace traditionally manufactured alternatives. According to James Wall, founder of Ireland’s leading provider of 3D printing solutions 3D Technology Ltd., the adoption of 3D printed parts is revolutionising the manufacturing industry.
“The benefits of 3D printing within a manufacturing environment are undeniable,” according to Wall. “We are seeing more and more leading Irish manufacturing companies adopting 3D printing as they seek to improve efficiencies and significantly reduce costs. In terms of quality and durability, meanwhile, 3D printed parts and products are now regularly outperforming traditionally manufactured alternatives.”
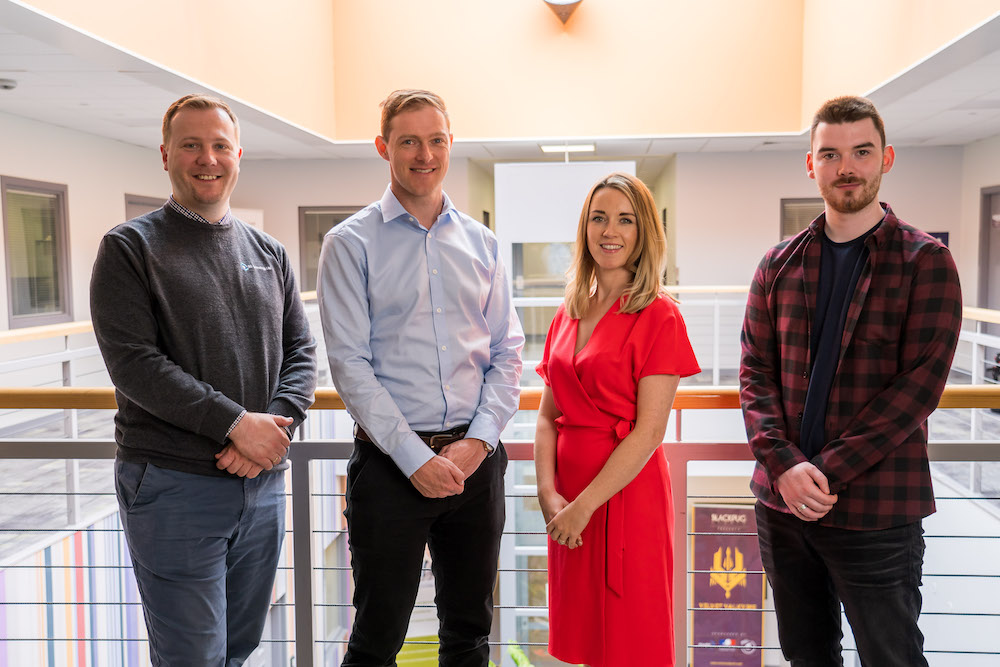
The Challenge
The STANLEY PD 45 is a high efficiency hydraulic post hole driver used by Stanley Infrastructure. To actuate the hydraulic driving mechanism, the device uses a group of ball bearings to transfer the trigger pull force into the hydraulic actuator. The actuator housing holds these bearings in series to transfer pull force around a bend. Each housing, meanwhile, is tested every time the operator pulls the trigger.
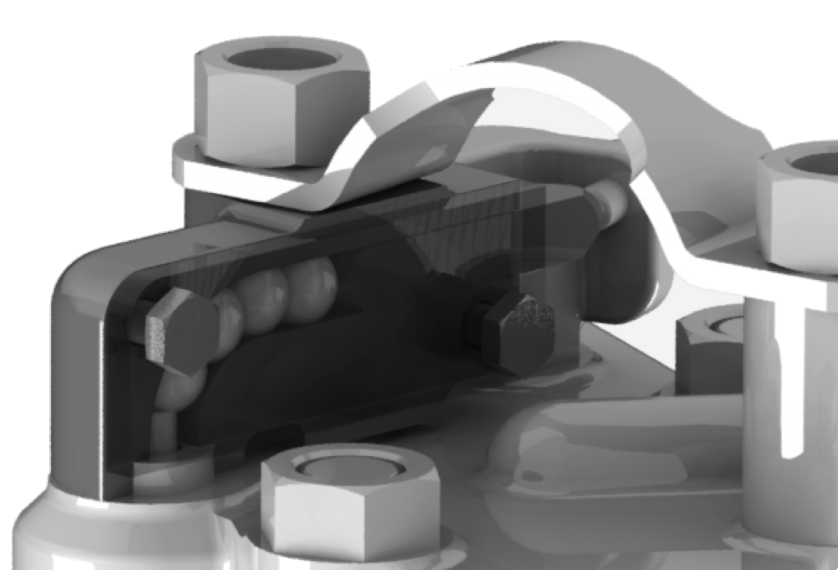
Original Part
The original actuator housing consisted of four parts – a cast and machined main housing, laser cut cover plate, and two bolts to fasten the housing assembly together.
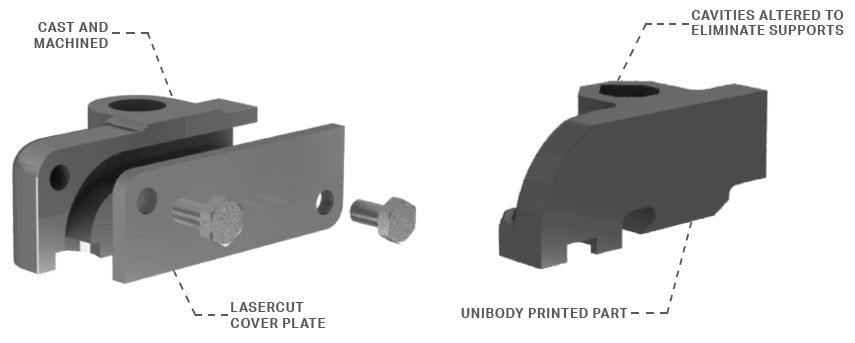
Markforged Part
Stanley Infrastructure engineers redesigned the part to print on the Markforged Metal X 3D printer. Instead of a four part assembly, the redesigned part prints in one piece without supports.
Physical Performance
Stanley Infrastructure tested three identical parts printed on the Metal X. These parts proved durable through tens of thousands of cycles and strong enough to handle significant compressive load while also being 53% lighter.
Cost Performance
By replacing their current manufacturing work flow with the Metal X, Stanley Infrastructure saves between 34% and 48% on manufacturing costs and slashes part lead time by 69%. While these are significant savings, they even better leverage the Metal X on single part manufacturing (in this case, Stanley Infrastructure often produces single replacement parts for devices in the field). Because their existing process only produces parts in batches, printing single parts with the Metal X is 12.5x cheaper and 20x faster than casting and machining. The Metal X further undercuts this process by being a pay-per-part machine instead of a pay-per-batch machine.
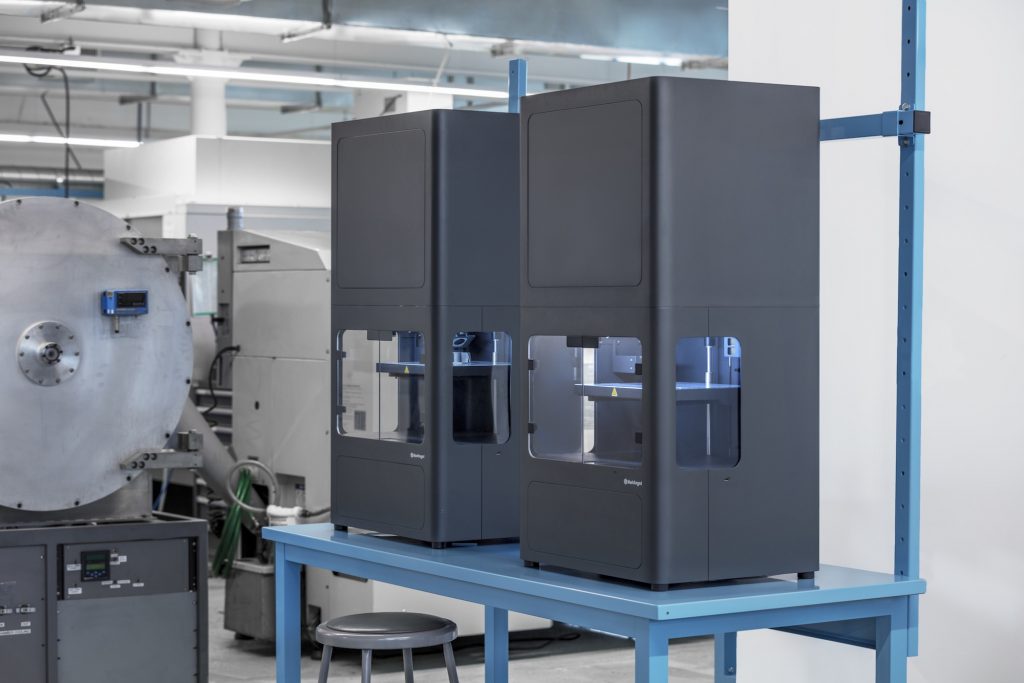
Analysis
According to a Stanley Infrastructure engineer, “it is very feasible to leverage the Metal X platform in additively manufacturing the discussed actuator housing with very minimal capital and time investment.”
Furthermore, Stanley believe that they can save thousands of dollars per year on this part alone, while replicating the part quality and reliability that they expect from machined parts.
To learn more about the Metal X 3D printer from Markforged, visit 3DTechnology.ie for more details.